Key Takeaways
- Importance of Regular Maintenance: Consistent upkeep of air compressors prevents unexpected failures, enhances performance, and extends equipment lifespan.
- Common Issues to Watch For: Be alert for signs such as pressure drops, overheating, and unusual noises that indicate potential problems needing attention.
- Essential Tools for Repair: Equip yourself with necessary tools like multimeters and torque wrenches to effectively diagnose and repair air compressor issues.
- Safety Considerations are Crucial: Always use personal protective equipment (PPE) and ensure all components meet safety standards during repairs to avoid accidents.
- Step-by-Step Repair Process: Follow a systematic approach for diagnosing problems and performing repairs to restore functionality efficiently.
- Recognising Early Warning Signs: Look out for unusual sounds, reduced airflow, or leaks that signal the need for immediate maintenance or repair.
Air compressor repair focuses on maintaining optimal performance and preventing costly equipment failures through regular maintenance and timely repairs. Common issues include pressure drops, overheating, and electrical faults that can disrupt industrial operations. Essential repair tools and safety equipment ensure effective diagnostics and secure working conditions during maintenance tasks. Compressor Systems provides comprehensive repair services across Australia, helping industries maintain reliable compressed air systems and minimise operational downtime.
Overview of Air Compressor Repair
Air compressor repair focuses on restoring functionality and efficiency in compressed air systems. Regular maintenance plays a crucial role in preventing costly breakdowns, ensuring optimal performance, and extending the lifespan of equipment.
Importance of Regular Maintenance
Regular maintenance safeguards against unexpected failures in air compressors. Scheduled inspections help identify wear or damage early, allowing for timely repairs that prevent larger issues. Routine tasks include checking oil levels, replacing filters, and inspecting hoses for leaks. In Perth, WA, industries like mining and automotive rely on consistent compressor operation; thus, preventative care enhances productivity and reduces downtime.
Common Issues with Air Compressors
Common issues affect air compressors across industries. Frequent problems include pressure drops due to leaks in the system or malfunctioning pressure regulators. Overheating may occur from insufficient lubrication or blocked cooling fins. Additionally, faulty electrical components can disrupt power supply to the compressor. Recognising these symptoms early facilitates quicker repairs and minimizes disruptions to operations in sectors such as food processing and manufacturing.
Tools and Equipment for Repair
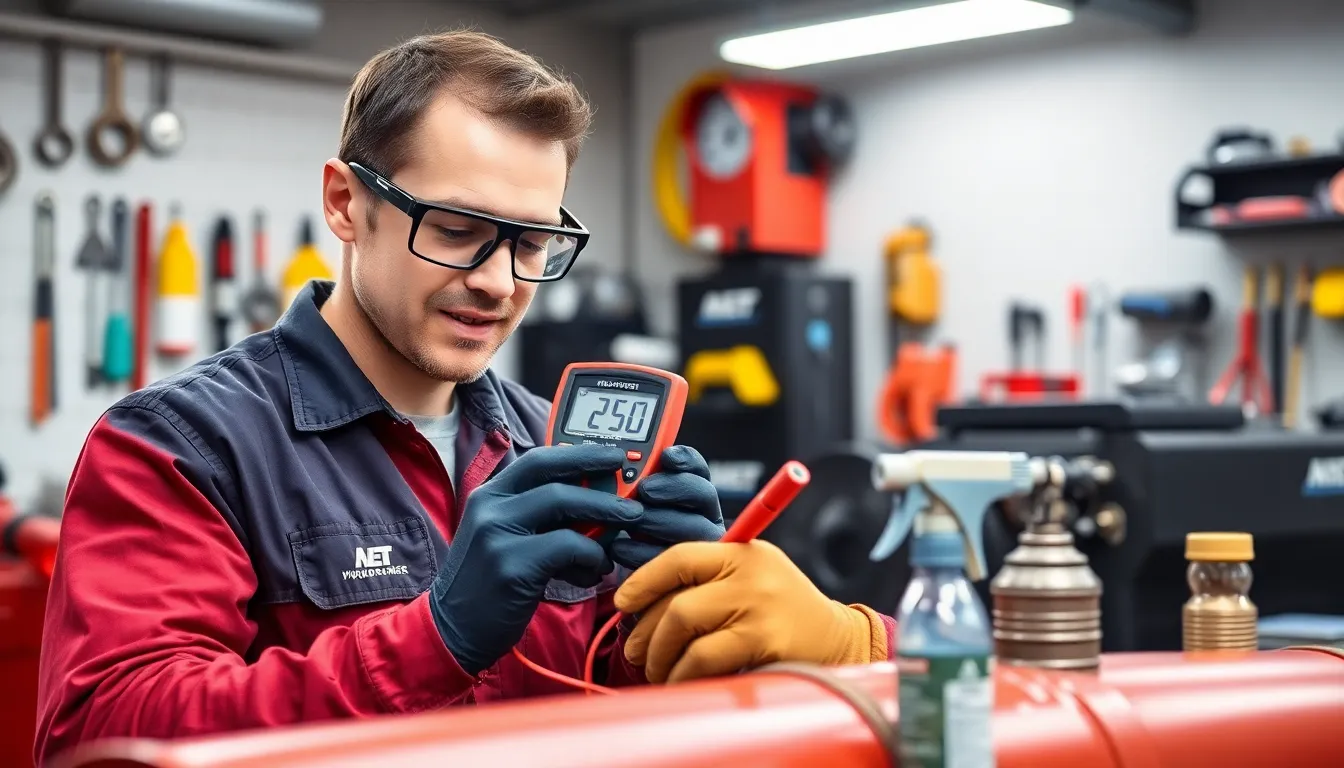
Effective air compressor repair relies on a set of essential tools and equipment. Proper tools improve diagnostic accuracy and repair efficiency, ensuring optimal performance.
Essential Tools for Air Compressor Repair
- Multimeter: Tests electrical components like pressure switches to confirm functionality.
- Soapy Water Spray Bottle: Detects air leaks by producing bubbles at hose connections.
- Compressed Air Source: Cleans air intake filters effectively, maintaining airflow.
- Mechanical Tools: Wrenches, screwdrivers, and hex drive bits are necessary for tightening bolts and replacing parts.
- Torque Wrench: Ensures proper tension on critical bolts such as head bolts to prevent failures.
- Replacement Parts: Includes hoses, valves, seals, piston rings, and oil crucial for maintenance.
These tools enable technicians to perform thorough repairs while minimizing downtime in industries reliant on compressed air systems.
Safety Equipment Considerations
Safety during air compressor repair is crucial. Key safety measures include:
- Use of Personal Protective Equipment (PPE) like safety goggles, gloves, and hearing protection to safeguard workers’ health.
- Ensuring all components (hoses, fittings) meet the compressor’s maximum pressure ratings to avoid accidents.
- Maintaining functional relief valves, which prevent overpressure; never bypass or remove these vital components.
- Keeping shutoff valves visible ensures easy access during emergencies or maintenance tasks.
- Installing guards around moving parts protects operators from potential injuries caused by flywheels or belts.
- Providing good workspace ventilation reduces risks associated with pollutants and carbon monoxide exposure.
Adhering to these safety considerations helps maintain a secure environment in facilities across Perth’s mining, automotive manufacturing, food processing, and industrial sectors.
Step-by-Step Repair Process
Repairing an air compressor involves a systematic approach to ensure safety and efficiency. Following specific steps aids in restoring functionality.
Diagnosing Problems
- Identify Symptoms and Possible Causes:
- Won’t Start: Check the power supply, oil level (for oil-lubricated models), and pressure switch function.
- Runs But No Pressure: Inspect hoses for leaks, examine piston rings or valves for wear, and check the air intake filter for blockages.
- Shuts Off Early: Investigate overheating due to poor ventilation or a faulty pressure switch.
- Excessive Noise/Vibration: Look for loose bolts, failing motor bearings, or worn pump parts.
- Check for Air Leaks: Spray diluted washing-up liquid around joints; bubbles indicate leaks.
- Advanced Diagnostics:
- Use vibration analysis to detect misalignment.
- Employ thermal imaging for overheating issues.
- Conduct noise analysis with specialized tools to pinpoint sources of sound.
Performing Common Repairs
- Air Leaks: Patch or replace faulty hoses and seals promptly to maintain system integrity.
- Electrical Repairs: Replace blown fuses, repair wiring faults, or swap out defective switches as necessary.
- Pressure and Valve Issues: Clean or replace malfunctioning pressure switches, valves, and filters regularly to ensure optimal operation.
- Mechanical Parts Maintenance: Replace worn piston rings, bearings, or belts; monitor performance closely during routine checks.
Regular adherence to these repair practices enhances compressor reliability in Perth’s mining, automotive manufacturing, food processing industries while reducing downtime effectively.
Preventative Measures
Preventative measures play a critical role in maintaining the efficiency and reliability of air compressor systems. Implementing regular checks can significantly reduce downtime and extend equipment lifespan.
Routine Maintenance Tips
- Daily: Check oil level, cooling airflow, belt tension, and safety guards. Empty condensate from tanks and verify pressure switch operation. Listen for unusual sounds during operation.
- Weekly: Inspect hoses and connections for signs of wear or damage. Clean or replace air filters to ensure optimal airflow. Check temperature and pressure dew point on models equipped with dryers.
- Monthly: Tighten bolts and fasteners to prevent loosening over time. Test safety relief valves to ensure they function correctly.
- Quarterly & Biannual: Change compressor oil and filters as per manufacturer recommendations. Assess valve function and tighten pulleys as needed.
Signs Your Compressor Needs Attention
Recognising early warning signs is essential for timely intervention:
- Unusual Noises or Vibrations: Indicate potential bearing wear or loose components that require immediate attention.
- Reduced Air Pressure or Flow: Suggest clogged filters, leaking hoses, or failing valves; addressing these issues promptly maintains performance.
- Oil or Air Leaks: Visible leaks around joints demand urgent repairs to prevent further damage.
- Overheating: An excessively hot compressor may signal cooling failures; checking ventilation is crucial.
- Frequent Cycling or Failure to Reach Pressure: Often points towards faulty pressure switches or persistent leaks needing resolution.
By adhering to these preventative measures, facilities across industries such as mining, automotive manufacturing, food processing, and others in Perth can improve system reliability while minimising disruptions.
About Compressor Systems
Compressor Systems offers a comprehensive range of compressed air services across Australia, providing solutions for installation, maintenance, and repairs for various compressor types and brands.
Under the leadership of Director Steve Chambers, the company specialises in pressure vessel inspections, air audits, leak testing, and maintaining a full inventory of spare parts to ensure optimal system performance. Compressor Systems is committed to energy-efficient solutions, providing tailored support to industries such as mining, automotive, food, and manufacturing. The company operates from multiple locations nationwide, including Perth, Melbourne, and Sydney, ensuring clients across Australia receive expert assistance.
Contact:
Steve Chambers, Director
Phone: 1300 183 355
Email: [email protected]
Website: www.compressorsystems.com.au
Frequently Asked Questions
What is the importance of air compressors in industries?
Air compressors are vital for various industries as they provide compressed air needed for tools, machinery, and processes. They enhance productivity and efficiency by powering equipment in sectors like mining, automotive, and manufacturing.
How can malfunctioning air compressors affect operations?
Malfunctioning air compressors can lead to costly downtime, reducing productivity and potentially impacting overall business operations. Early identification of issues helps prevent prolonged disruptions.
Why is regular maintenance crucial for air compressors?
Regular maintenance ensures optimal performance and longevity of air compressors. It allows for early detection of wear or damage, preventing unexpected failures that could disrupt operations.
What common issues do air compressors face?
Common issues include pressure drops, overheating, electrical faults, and leaks. Recognising these symptoms early on can facilitate quicker repairs and minimise operational interruptions.
What tools are essential for effective air compressor repair?
Essential tools include multimeters for electrical diagnostics, soapy water spray bottles to detect leaks, and mechanical tools for repairs. These improve diagnostic accuracy and repair efficiency.
How should safety be considered during compressor repairs?
Safety measures include using personal protective equipment (PPE), ensuring components meet pressure ratings, and maintaining functional relief valves. This ensures a secure environment during maintenance tasks.
What are some routine maintenance tips for air compressors?
Routine tips include daily oil level checks, weekly inspections of hoses/filters, and monthly bolt tightening. Following these practices enhances reliability while minimising potential disruptions.
When should I seek professional help for my compressor issues?
Seek professional help if you encounter complex problems beyond basic troubleshooting or if your compressor shows persistent signs like unusual noises or frequent cycling despite routine checks.