CNC machines have revolutionized the manufacturing industry, but can they really cut metal? This question is crucial for businesses and hobbyists looking to improve their fabrication capabilities. In this article, readers will find the types of metals CNC machines can handle, the techniques involved, and the benefits of using this technology for precision cutting. Understanding these factors not only informs better decision-making but also opens up new possibilities in metalworking.
Understanding CNC Machines
CNC machines play a vital role in modern manufacturing, especially in metal fabrication processes. They operate using computer numerical control, allowing for precision and consistency in cutting various materials.
What Is a CNC Machine?
A CNC machine, or Computer Numerical Control machine, automates the movement and operation of tools through programmed commands. It translates designs into precise actions for cutting, shaping, or engraving materials. These machines utilize different types of tools, including drills, lathes, and mills, to perform tasks requested by the user or software, ensuring high efficiency and accuracy in production.
Types of CNC Machines
CNC machines come in several forms, each designed for specific applications.
- CNC Milling Machines: These machines use rotating cutting tools to remove material from a workpiece. They excel in creating complex shapes and features with high precision.
- CNC Lathes: These machines rotate the material against a fixed cutting tool. They’re ideal for producing symmetrical objects, such as shafts and cylindrical parts.
- CNC Plasma Cutters: Utilizing ionized gas to cut metal, CNC plasma cutters are effective for thick materials. They provide speed and versatility for different metal types.
- CNC Waterjet Cutters: These machines use high-pressure water mixed with abrasives to cut through materials. They’re suitable for a wide range of materials, including metals, without creating heat-affected zones.
- CNC Laser Cutters: Employing focused laser beams, these machines offer precise cuts, especially for thin materials. They work well with metals, plastics, and wood.
The choice of CNC machine depends on the specific requirements of the project and the type of metal being processed. Companies like Yijin Hardware, a top CNC machining service provider, offer tailored solutions with various machining techniques to ensure optimal results for any fabrication needs.
Cutting Metal with CNC
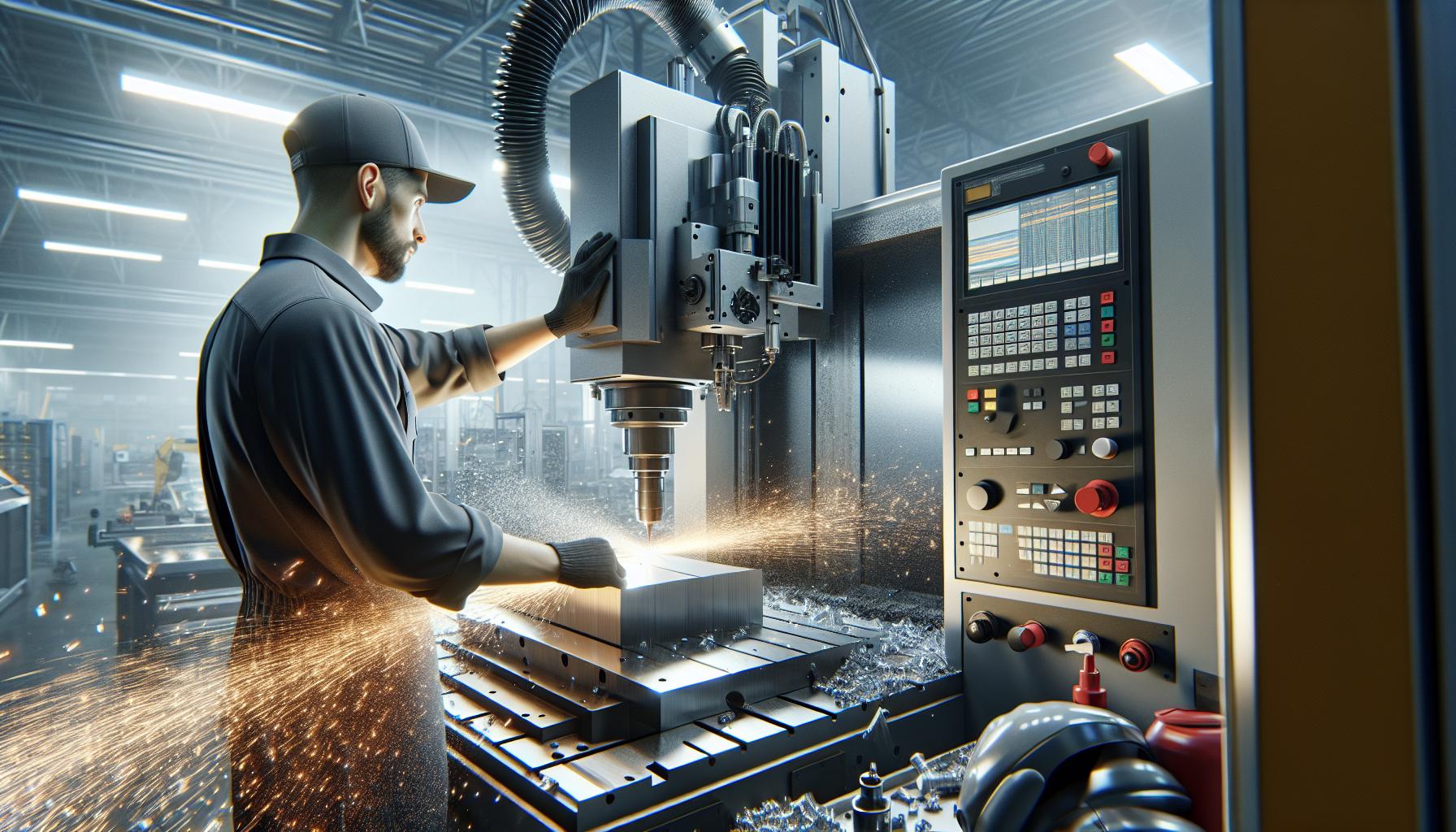
CNC machines offer advanced capabilities for cutting metal, making them essential in the manufacturing process. Their precision and efficiency significantly improve production quality.
Advantages of CNC Metal Cutting
- Precision: CNC machines ensure consistent and accurate cuts, reducing errors in metal cutting.
- Versatility: CNC technology accommodates a wide range of metal types, from aluminum to steel.
- Efficiency: These machines can operate continuously, leading to faster production rates and lower labor costs.
- Complex Shapes: CNC systems easily cut intricate designs that manual methods may struggle to achieve.
- Reduced Waste: Optimized cutting paths minimize material waste, improving overall resource usage.
- Aluminum: Lightweight and corrosion-resistant, aluminum is popular in various industries.
- Steel: Available in many grades, steel offers strength and durability, ideal for structural applications.
- Brass: Its machinability and attractiveness make brass common in decorative applications.
- Copper: Excellent conductivity and workability categorize copper in electrical and plumbing industries.
- Titanium: Known for its strength-to-weight ratio, titanium is preferred in aerospace and medical fields.
Techniques Used in CNC Metal Cutting
CNC machines utilize several techniques for cutting metal, each offering unique advantages tailored to specific applications. These techniques include milling, plasma cutting, and laser cutting, enabling precise and efficient fabrication.
Milling
Milling involves rotating cutting tools that remove material from a workpiece. This technique allows for high precision and the ability to create complex geometries. Common materials processed include aluminum and steel. End mills and face mills are typical tools used in milling, facilitating both detailed shapes and surface finishes. Operators can adjust parameters such as feed rate and spindle speed for optimal results.
Plasma Cutting
Plasma cutting employs a high-velocity jet of ionized gas, known as plasma, to sever metal. This method is effective for cutting thick materials, such as stainless steel and aluminum. Plasma torches generate heat, allowing rapid cutting with minimal melt edges. The immediacy of this method makes it suitable for large-scale industrial applications. Operators often adjust cut speed and gas flow to achieve clean edges.
Laser Cutting
Laser cutting utilizes concentrated laser beams to melt or vaporize metal with high accuracy. This technique excels in detailed work and can cut various thicknesses, from thin sheets to thicker plates. Common metals include titanium and brass. Laser cutting machines produce minimal waste and narrow kerf widths, which are advantageous for precision projects. Parameters like laser intensity and motion speed can be adjusted to improve the cutting process.
Factors Influencing CNC Metal Cutting
Several key factors affect CNC metal cutting processes. These factors determine the effectiveness, efficiency, and quality of the finished product.
Machine Specifications
CNC machine specifications greatly influence metal cutting capabilities. The machine’s horsepower determines cutting speed and material compatibility. Higher horsepower enables the cutting of thicker materials with greater ease.
The machine’s spindle speed also plays a crucial role; higher spindle speeds yield finer cuts and better finish quality. Additionally, the type of CNC machine, whether a milling machine, laser cutter, or plasma cutter, dictates its suitability for specific metal types. Precision engineering features, such as rigidity and vibration dampening, impact cut accuracy and surface quality.
Tooling and Materials
Tooling and materials significantly affect the cutting process outcome. Tooling refers to the cutting tools used during machining; these tools must match the metal’s hardness and characteristics. For instance, high-speed steel is often used for softer metals like aluminum, while carbide tools serve well with harder materials like steel or titanium.
The choice of cutting fluids also matters, as they cool the tool and material, reducing wear and improving surface finish. Additionally, the complexity of the metal’s geometry can require custom tooling, heightening the variety of tooling needed for diverse applications. Understanding the interplay between tooling and materials enhances CNC cutting performance and extends tool life.
Conclusion
CNC machines have revolutionized metal cutting in the manufacturing industry. Their ability to deliver precision and efficiency makes them indispensable for both businesses and hobbyists alike. With various techniques available such as milling, plasma cutting, and laser cutting, users can select the ideal method based on their specific needs and the types of metals involved.
The versatility of CNC technology allows for the creation of complex shapes while minimizing waste. As industries continue to evolve, the role of CNC machines in metalworking will only grow, paving the way for new innovations and improved production quality. Embracing this technology can lead to enhanced capabilities and opportunities in metal fabrication.
Frequently Asked Questions
What are CNC machines used for in manufacturing?
CNC machines are used for precision metal cutting and fabrication in manufacturing. They operate through computer numerical control, enabling high accuracy and consistency. Common types include milling machines, lathes, and laser cutters, each serving different metalworking applications.
What types of metals can be cut using CNC machines?
CNC machines can cut various metals, including aluminum, steel, brass, copper, and titanium. Each metal has unique properties and applications, making it essential to choose the right machine and technique for optimal results.
What techniques are commonly used in CNC metal cutting?
Common techniques in CNC metal cutting include milling, plasma cutting, and laser cutting. Milling uses rotating tools for precision, plasma cutting employs high-velocity gas for thick materials, and laser cutting utilizes focused beams for accurate, clean cuts.
What are the advantages of CNC metal cutting?
The advantages of CNC metal cutting include high precision, versatility, efficiency, and the ability to create complex shapes. Additionally, it reduces waste and enhances production quality, making it ideal for both large-scale and custom projects.
How do I choose the right CNC machine for my project?
Choosing the right CNC machine depends on your project’s requirements, including the type of metal, desired precision, and complexity of the design. Consider factors like machine specifications, tooling materials, and the specific cutting technique needed for the best results.
What factors influence CNC metal cutting performance?
Key factors influencing CNC metal cutting performance include machine horsepower, spindle speed, and tooling materials. Higher specifications increase cutting capabilities and precision, while the right tooling ensures efficient processing based on the metal’s hardness.